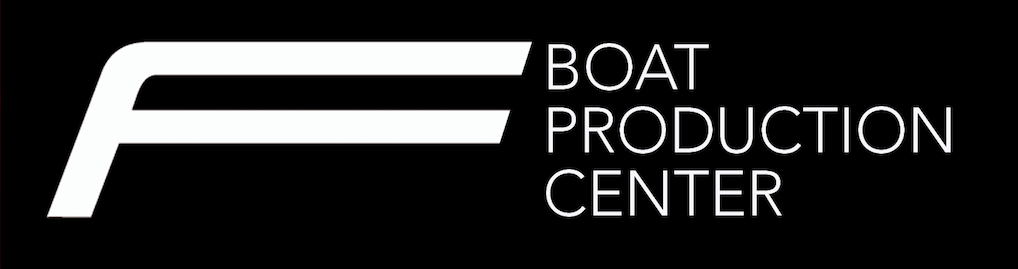
Innovation
and
technology
and
technology
F Boat Production Center has modern facilities in Gador (Almería), with the latest design technology, modeling, painting, lamination and mounting of exclusive boats. It also has an excellent distribution network and national and international after‐sales service integrated with nautical leaders in each area.
The important human capital formed by the naval engineers, designers, electricians, carpenters, modelers, plumbers… works in the achievement of FAETON ́s firm commitment: the excellence of its boats.
The technology applied to automate the productive process is developed in relation with the quality demands of F Boat Production Center, and is in constant evolution. The facilities are a reflection of this demand.
DIVISIONS
- Administrative and commercial.
- Engineering and design.
- Cutting mounting and upholstery.
- Finishes.
- Quality control.
- Delivery and post sales service.
FACILITIES
- Polishing of stainless steel.
- Resin distribution.
- Mounting of electrical panels.
- Mounting and supervision of mechanics.
- Mounting and supervision of hydraulics.
- Special lacquer cabin.
- Carpentry and cabinetmaker workshop.
- Numerical control cabin.
THE COMPLETE PRODUCTION PROCESS
1∙ MOLDS:
Molds are produced from a model using a milling machine with a 6 axis numerical control. Afterwards they are sanded, polished and cleaned.
2∙ PAINTING:
In the painting cabin, a layer of high‐quality vinelester resin based gel coat is applied to the mold to create the desired colour. Factors that must be controlled in order to obtain the best results are: suitable temperature conditions, humidity, optimum state of painting, correct catalyzing, appropriate thickness of the paint layers.
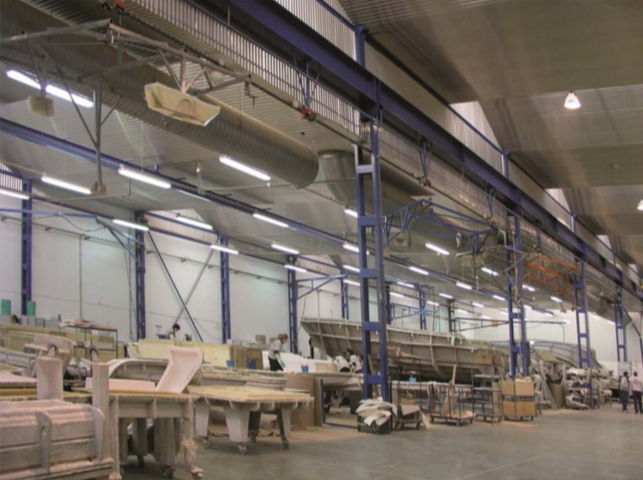
3∙ LAMINATION:
The glass fiber and resin are applied on top of the gel coat in addition to the necessary nuclei needed to reinforce and give both consistency to the structure and resistance against torsion. This operation is done using the traditional method (manually) or using infusion. A series of factors are controlled, such as: the temperature and humidity conditions, control of catalyzing of the resin and ideal thickness of the layers, a fundamental factor since it will influence the navigability of the boat.
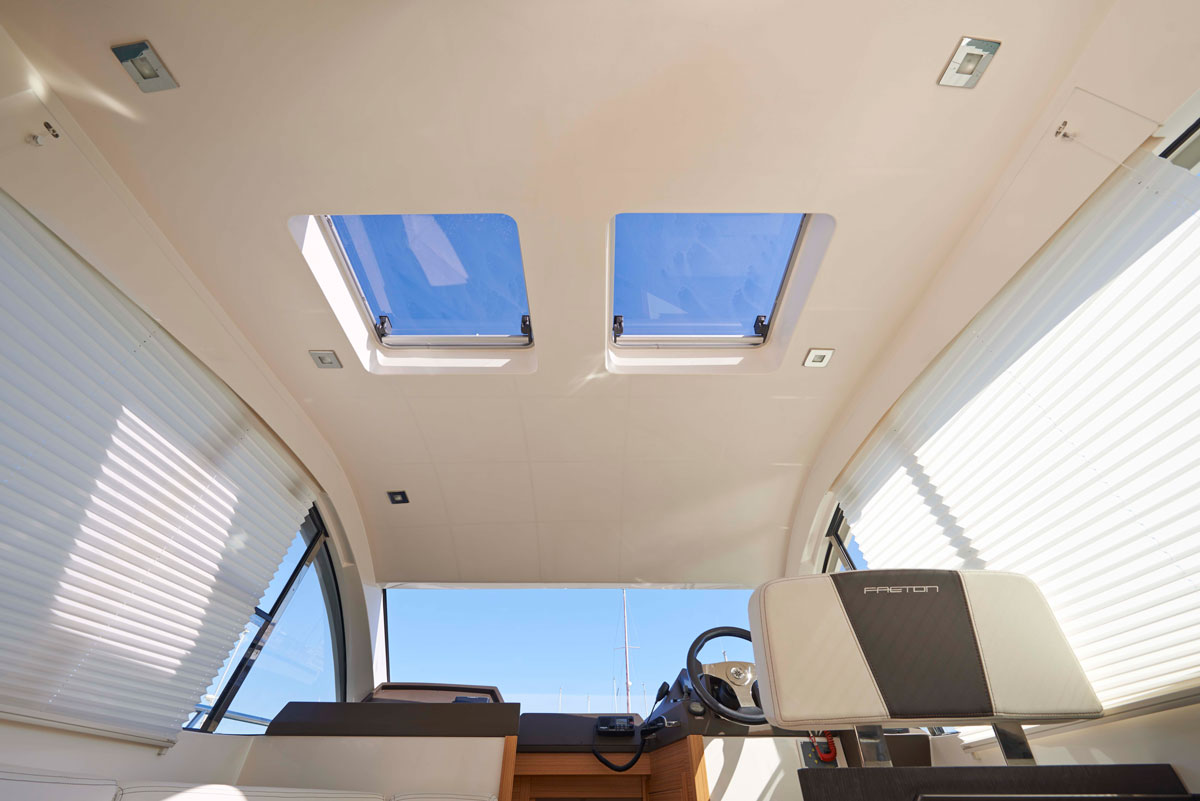
4∙ CUTTING:
In the cutting cabin all the fiber burrs and spaces are cut with an aspiration and filtration system that complies with the environmental standards of health and safety.
5. MOUNTING:
The hull and the deck enter in the assembly warehouse where the motor and the electrical components are installed and the carpentry operations… and the subsequent assembly of components carried out. All components fit together perfectly offering perfect silent and vibration free navigation.
QUALITY ASSURED AND GUARANTEED
Every FAETON boat passes an individual procedure of quality control and certification. The process consists of following a protocol of tests designed to assure maximum quality in the boats. This traceability protocol (it creates an history for every boat that is registered) is always executed in “water” checking the start‐up of motors, circuits of freshwater, saltwater and wastewater, tightness tests of portholes, trapdoors, windscreens, thru‐hull fittings etc. The finishes are also checked i.e. the state of polyester, carpentry, and upholstery. As a proof of quality FAETON offer a two year guarantee.
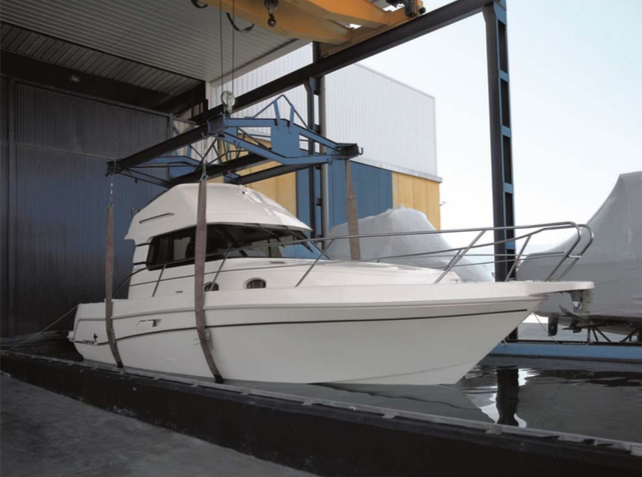
FAETON WITH THE ENVIRONMENT.
The environment is fundamental in the construction of FAETON boats.
Under these premises FAETON intends to offer the greatest environmental benefits e.g. sustainable navigation and researching the most efficient forms of compensation for CO2 emission, to correctly eliminate the waste generated during boat production.
CURRENTLY
Currently, Faeton has diversified its activity, in addition to manufacturing our own brand, we have been building boats for other shipyards for four years, such as the entire RAND BOATS range and the Astondoa 377 Coupe model.
However, our production capacity is higher than what we are currently dealing with, so I wanted to propose to you the possibility of manufacturing some or some of its models, be they the largest and most complicated models, in which we have the necessary quality to defend the product up to 40 feet, or failing the most requested models, since we have the possibility of manufacturing modes autonomously and molds could be duplicated to address a large number of units per year.